myBuddy, a Dual-Arm Collaborative Robot Powered by Raspberry Pi
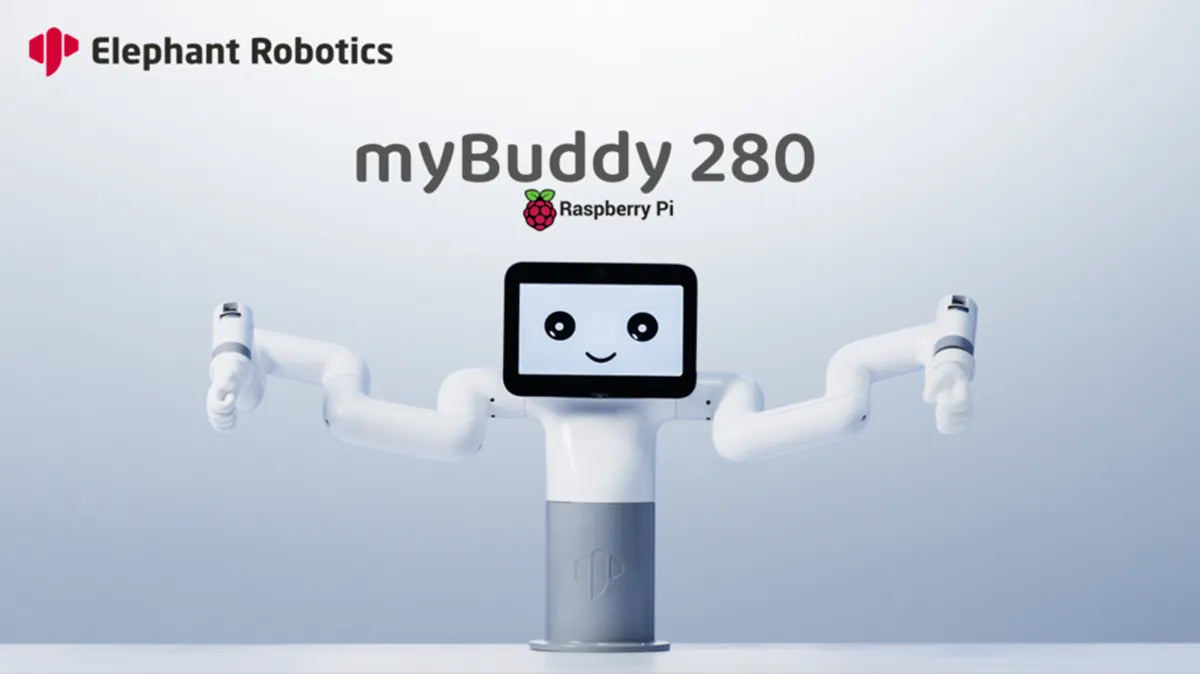
In July 2022, Elephant Robotics released myBuddy—a dual-arm, 13-axis humanoid collaborative robot powered by Raspberry Pi with multiple functions—at an incredible price. It works with multiple accessories such as suction pumps, grippers, and more. Additionally, users can boost their secondary development with the artificial intelligence and myAGV kits and detailed tutorials published by Elephant Robotics. myBuddy helps users achieve more applications and developments as a collaborative robotic arm.
Elephant Robotics has been committed to R&D, manufacturing, and producing collaborative robots, such as myCobot, mechArm, myPalletizer, and myAGV. To meet the expectations of users from more than 50 countries worldwide and allow everyone to enjoy the world of robotics, Elephant Robotics is achieving more breakthroughs in product R&D ability and manufacturing capacity.
In 2020, the team of Elephant Robotics found that the need for robotics applications was increasing, so they decided to produce a robot with multiple functions that could meet more requirements. In the development and production process, the team met many difficulties. At least three auxiliary control chips were needed to develop more functions, increasing the production difficulty by more than 300 percent compared to myCobot, a 6-axis collaborative robot (cobot). The biggest problem was how to make a robot with multiple functions at an affordable and reasonable price.
After more than two years of continuous efforts, Elephant Robotics has upgraded the myCobot series and transferred it to the new myBuddy cobot based on its highly integrated product design and self-developed robot control platform. The product design of myBuddy is based on the myCobot series combined rounded corners, and the overall industrial design style is simple and beautiful. A robot at an affordable price makes the development of dual-arm cobot applications no longer a problem.
Get to know what applications myBuddy can achieve through the features and functional analysis.
Compact size with more flexibility
The working radius of a single arm of myBuddy is 280 millimeters, and the maximum payload is 250 grams. It is light and flexible, with 13 degrees of freedom. The built-in axis in the torso of myBuddy improves the working range by more than 400 percent compared to myCobot's single robotic arm, so it can perform more complicated tasks such as flag waving, kinematics practice, and AI recognition.
Independent open-source, secondary development support
There are more than 100 API interfaces that can be used, and the bottom control interfaces of myBuddy are open. The potential value, angles, coordinates, running speeds, and other interfaces can be controlled freely, so users can master the application research of dual-arm robots, motion path planning, development of action, and visual recognition. On the hardware interface, myBuddy provides a variety of input and output interfaces, including HDMI, USB, Grove, 3.3V IO, LEGO, RJ45 interface, and more.
In the software, myBuddy supports multiple programming environments. myBlockly, a visual tool with multiple built-in robot application cases for graphical programming, simple and easy for users to use and develop their projects. Users can also control myBuddy in Python and set the joint angle and robot coordinates, and get the speed position in real-time (response time up to 20 milliseconds). Moreover, myBuddy supports the simulation development environment ROS. With the built-in ROS environment, users can realize robot motion path planning algorithm research, dual-arm interference avoidance algorithm research, robot vision learning, and other artificial intelligence application development.
Deep learning in robot vision & VR control
myBuddy has a 7-inch interactive display screen, two 2-million-pixel HD cameras, and more than 20 built-in dynamic facial expressions. Users can conduct scientific research in human-robot interaction, robot vision, robotics learning, artificial intelligence, action planning, mechatronics, manufacturing, and automation with myBuddy. The built-in cameras support area location positioning, object, and QR code recognition. myBuddy can achieve face and body recognition, motion simulation, and trajectory tracking with the cameras.
With fast, high-tech development, VR technology is beginning to become an area of independent research and development, so Elephant Robotics decided to build a VR wireless control function into myBuddy. In this function, users can not only experience human-robot interaction and carry out some dangerous scientific experiments, they can also explore more principles and basic applications of wireless control in cobots, such as underwater exploration, remotely-piloted vehicles, and space exploration. In the future, myBuddy can be used as a surgeon in the support of a virtual surgical system.
Dual-arm collaboration with multiple accessories
Elephant Robotics has developed more than 20 robotic arm accessories, including an end-effector, base, camera, mobile phone gripper, and more. myBuddy has more flexibility, maneuverability, and load capacity than myCobot's single robotic arm. The ability to grasp and move objects has been effectively improved in both rigid and flexible objects and effectively avoids any collisions between the two arms when working. With these accessories, myBuddy can perform more applications in science and education. For example, after installing a gripper and a suction pump, myBuddy can grab test tubes and pour liquids.
A dual-arm robot at an affordable price is a preferred choice for many individual developers, especially teachers and students in robotics and engineering. myBuddy, with its multiple functions supported, will help people explore and develop more possibilities in the world of robotics.
myBuddy 280-Pi | The most compact collaborative Dual-arm robot in the world
-
Posted in
Comsumer Robots