How to Choose a Desktop 6-axis Robotic Arm for Beginners?
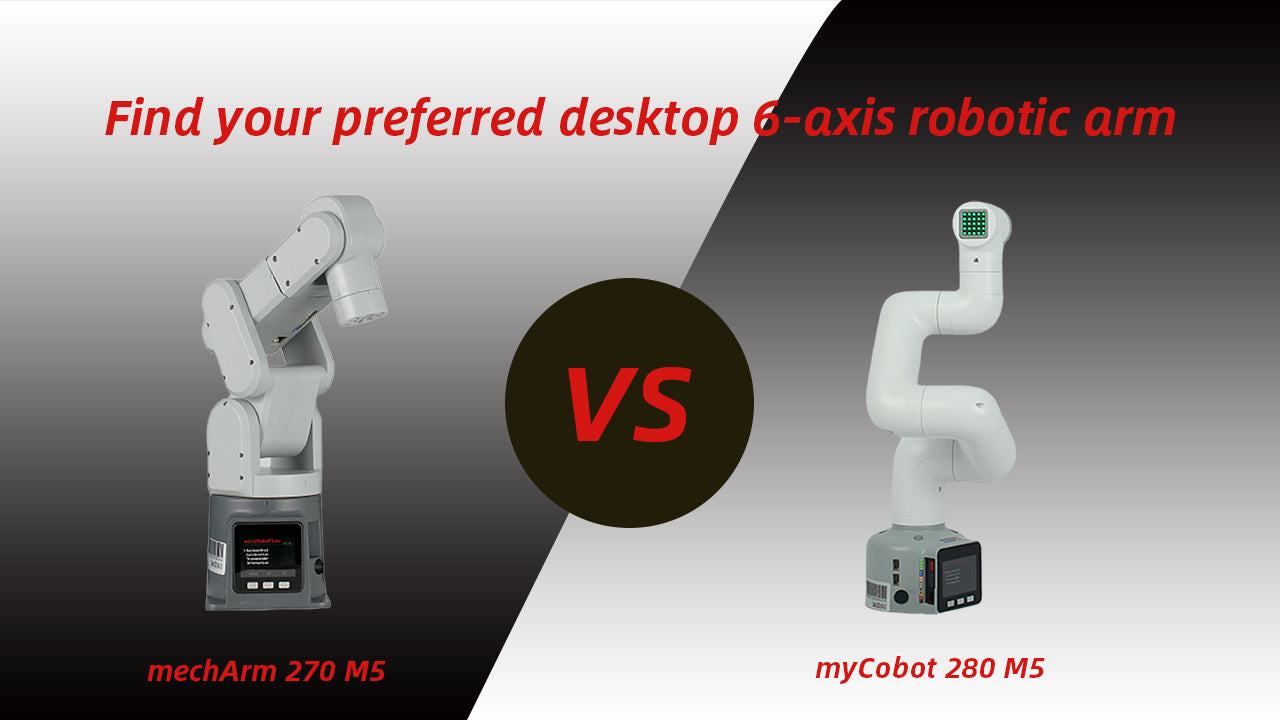
Learning Robotics with Educational Robots
In today's rapidly evolving technological landscape, the rise of automation is inevitable, leading to a growing interest in robotic arms. Before diving into complex industrial robots, learning from educational robots is a fantastic way to get started. There are many robotic arms for education and science research, how do we choose in the robotics market?
In this, we'll provide two small desktop six-axis robotic arms ideal for beginners who want to learn robotics and build prototypes quickly. We'll compare these two robots and help you find the best one for your needs.
Inside this Article:
What is the difference between an industrial robot and a collaborative robot?
Industrial robotic arms
Industrial robots excel at high-speed, heavy-duty tasks in hazardous environments. This translates to increased production output, reduced operational costs for companies, and improved worker safety by eliminating human interaction with dangerous tasks. It should be noted that industrial robots are often installed in secured areas like cages to ensure safety due to their powerful movements.
Collaborative robotic arms
Unlike their industrial counterparts, collaborative robots are smaller, lighter, and equipped with safety features like sensors and force control. This allows them to work safely alongside humans, making them ideal for collaborative tasks.
Why choose a desktop robotic arm?
Small desk robots are designed specifically for learning purposes. They are affordable and easy to use. Support picking and placing, motion control, visual tracking and more.
- Most industrial robotic arms are in centrosymmetric structure, and collaborative robotic arms are in cobot structure.
myCobot 280 M5Stack
myCobot 280 has 4 versions, M5 Stack is a 6-axis collaborative robot powered by M5Stack-Basic with multiple functions, it is designed with a cobot structure.
mechArm 270 M5Stack
mechArm 270 M5 Stack is similar to myCobot, but the structure of mechArm is centrosymmetric.
Development and Programming Options
Both myCobot and mechArm allow users to quickly set up a development environment and learn arm control logic. They support popular programming languages like Python, C++, C#, and JavaScript. Elephant Robotics provides a Gitbook for quickly building a robotic arm development environment with detailed tutorials on everything from setting up the environment to controlling the robotic arm.
ROS Demo
Use slider to control myCobot.
MoveIt for programming, enabling path planning and obstacle avoidance.
They can be integrated with an AI Kit., enabling users to explore concepts like machine vision and robot arm coordination for tasks like object recognition and grasping.
- The interfaces on the end of the robotic arm are the LEGO interfaces, we can use the accessories from Elephant Robotics or make by ourselves through 3D printing to complete our development needs.
myCobot vs. mechArm
Let's look at their configuration. What's Difference?
Specification | mechArm 270 M5 | myCobot 280 M5 |
---|---|---|
Structure | Centrosymmetric | Cobot |
Degree of Freedom | 6 | 6 |
Payload | 250g | 250g |
Working Radius | 270mm | 280mm |
Positioning Accuracy | ±0.5 mm | ±0.5 mm |
Weight | 1000g | 850g |
Master Core | ESP32 | ESP32 |
Steering Gear Type | High performance servo motor | High performance servo motor |
Main Frequency | 240MHz dual core | 240MHz dual core |
Computing Performance | 600DMIPS | 600DMIPS |
Working Lifespan | 500h | 500h |
SRAM | 520KB | 520KB |
Bluetooth | Dual mode Bluetooth 2.4G/5G | Dual mode Bluetooth 2.4G/5G |
Core Flash | 4M | 4M |
Programming | Python, C++, C#, JavaScript | Python, C++, C#, JavaScript |
Joint Rotation Speed | J1: -165°~+165° J2: -90°~+90° J3: -180°~+65° J4: -165°~+165° J5: -115°~+115° J6: -175°~+175° |
J1: -168°~+168° J2: -135°~+135° J3: -150°~+150° J4: -145°~+145° J5: -165°~+165° J6: -180°~+180° |
- The differences in working radius, positioning accuracy, and range of joint movements are due to their different structures.
Structure and Stability
- Centrosymmetric Structure (mechArm): This is the most widely used structure for industrial robots. MechArm's joints 2, 3, and 4 benefit from bilateral support, offering greater stability and smoother movements.
- Cobot Structure (myCobot): The UR structure allows for a wider working radius and more flexible movement due to the lack of a central support column. However, this flexibility can lead to slight deviations in movement compared to the centrosymmetric design as without the holding, the robotic arm needs to rely on the motors to keep stable.
Joint Rotation Range
mechArm
myCobot
- mechArm is limited in terms of movement, myCobot is more flexible.
Making Your Choice
Specification | mechArm 270 M5 | myCobot 280 M5 |
---|---|---|
Structure | Centrosymmetric | Cobot |
Degree of Freedom | 6 | 6 |
Positioning Accuracy | ±0.5 mm | ±0.5 mm |
Payload | 250g | 250g |
Working Radius | 270mm | 280mm |
Joint Rotation Speed | J1: -165°~+165° J2: -90°~+90° J3: -180°~+65° J4: -165°~+165° J5: -115°~+115° J6: -175°~+175° |
J1: -168°~+168° J2: -135°~+135° J3: -150°~+150° J4: -145°~+145° J5: -165°~+165° J6: -180°~+180° |
Structure and Stability of Movement | Better | Normal |
Flexibility | Normal | Better |
Choices for Beginners | Better | Better |
Scenarios | Education Research Learning the principles of robotic arms Industrial robotic arm scenarios Machine Vision |
Education Research Learning the principles of robotic arms Collaborative robotic arm scenario Machine Vision |
- Choose myCobot if: You prioritize flexibility and human-machine collaboration scenarios.
- Choose mechArm if: You prioritize stability and learning in the direction of industrial robotic arms.
For beginners, desktop robotic arms offer a perfect entry point into the world of robotics. Both are 6-axis robotic arms designed for educational and personal use.