Exploring Innovations in Robotics: Range Applications of Cobots and AGVs
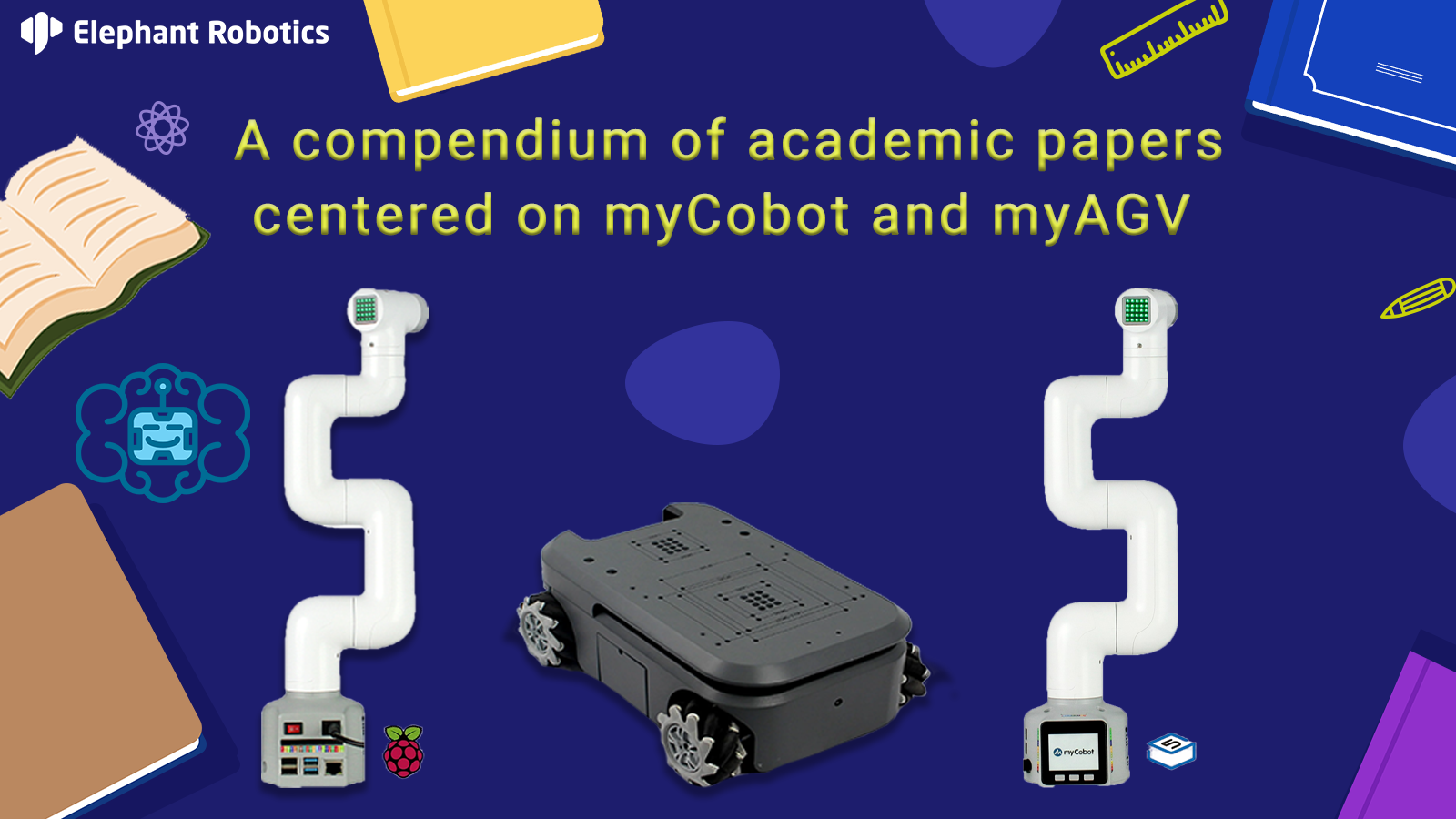
In the ever-evolving landscape of robotics, the symbiosis between humans and machines takes center stage, marking the advent of a new era of innovation. Today, we are thrilled to introduce a pioneering collection of academic papers focusing on Collaborative Robots (Cobots) and Automated Guided Vehicles (AGVs) sourced from prestigious global universities,such as The University of Sydney, Purdue University and Meijo University. This compilation delves into the transformative capabilities of Elephant Robotics' 6 DOF collaborative robots, myCobot series, and myAGV, exploring the practical applications and potential advancements in human-machine collaboration.
The comprehensive collection of 18 academic papers unveils profound insights across 3 pivotal dimensions. It delves into the forefront of artificial intelligence and explores the intricacies of robotics, encompassing deep learning, machine vision, robotic arms, programming, human-robot collaboration, and real-time monitoring. Additionally, it sheds light on advanced robot systems, including modular robots, reconfigurable robots, educational robots, and mobile robots with a specific emphasis on SLAM navigation. It stands as a valuable knowledge repository, offering a multidimensional perspective on the advancements and applications within the fields of Cobots and AGVs. Tailored to enthusiasts, professionals, and researchers, this collection is an invaluable resource for staying informed about the latest developments and innovations in the dynamic realm of robotics.
Topic: AUTOMATION OF THE QUALITY CONTROL PROCESS WITH THE USE OF ROBOTICS AND A COORDINATE MEASURING MACHINE
Author: Alexander Hoang
University: Purdue University
Abstract: The research project explored the feasibility for MSMEs to integrate a robotic arm into a low-volume production line for seamless part transfer to a quality control system. The process aimed at achieving automatic quality control without disrupting manufacturing. It involved an injection molding machine producing parts, and a collaborative robotic system transferring these parts to a CMM for inspection. The study demonstrated that constructing an automated quality control work cell was effective for MSMEs, with the main tasks being programming the robotic arm myCobot 320 M5 and designing the work cell. The system consistently met metrics for realignment, movement, and inspection routines, showcasing its effectiveness, adaptability, and modularity. Recommendations included using different IDEs, incorporating a vision system, and testing with various components for versatility.Topic: High-throughput fabrication of soft magneto-origami machines
Author: Shengzhu Yi 1,7, Liu Wang 2,7, Zhipeng Chen 1,7, Jian Wang 1, Xingyi Song 1, Pengfei Liu 1, Yuanxi Zhang 1, Qingqing Luo 1, Lelun Peng 1, Zhigang Wu 3, Chuan Fei Guo 4,5,6 & Lelun Jiang 1
Abstract: The research introduces a fabrication strategy for soft magneto-active machines, enabling magnetically controllable shape-morphing and locomotion, with applications in biomedical robotics. The proposed approach utilizes origami folding to transform 2D magnetic sheets into 3D soft magneto-active machines through automated roll-to-roll processing. The study demonstrates applications such as a collaborate robot myCobot Pro 600 with on-demand deploying and wireless charging, a mechanical encoder, a quadruped robot for cargo-release tasks, and a magneto-origami arts/craft. The incorporation of origami principles allows for efficient creation of complex structures with customized geometries. The magnetic sheet retains foldability while providing magnetic responsiveness. The research addresses the need for automated origami folding for consistent shape and performance, suggesting future work on developing an automated line for folding origami with uniform results.Topic: A Jacobian vector correction method for the force calibration of EIT-based tactile sensor
Author: Haofeng Chen, Xuanxuan Yang, Gang Ma, Xiaojie Wang
Abstract: This paper introduces a Jacobian vector correction (JVC) method for calibrating tactile force in EIT-based tactile sensors. The JVC method effectively addresses non-uniform sensitivity distribution by constructing a scaling vector based on the Jacobian vector, ensuring approximately constant sensitivity across all sensor locations. Phantom experiments of myCobot and sensor calibration evaluations validate the method's accuracy in capturing strength information independent of location. The JVC method enhances the practicality and applicability of EIT-based tactile sensors, offering precise force calibration with minimal data and control parameters. This improvement in force sensing capabilities makes EIT-based tactile sensors valuable for applications such as safe human-robot interactions.
Topic: Integration of proximity sensors in commercial robotic arm
Author: Gurwinder Singh Rani
University: Universitat Politècnica de Catalunya
Abstract: The project involves integrating 6 proximity sensors into a commercial robotic arm, specifically the MyCobot 320 Pi, providing it with 6 DOF for enhanced environmental interaction. The project includes learning the robot's basic operation, conducting electronics tests, and designing components to hold sensors and control electronics. Programming is implemented to control the robot and handle sensor data, allowing seamless integration of sensor feedback into the robot's actions. The project demonstrated effective obstacle detection and trajectory pausing, fulfilling its objectives that the 6 sensors effectively detect objects within their range and pause the robot's trajectory when necessary and solving challenges such as I2C errors and initial design flaws.Topic: Vision-Based Robot Arm Control Interface for Retrieving Objects from the Floor
Author: Laijun Yang 1, Ryota Sakamoto 2, Norihiko Kato 1, and Ken’ichi Yano 1
University: Mie University
Abstract: This study addresses the challenges faced by individuals with high-level spinal cord injuries, especially those with trunk dysfunction, when picking up objects from the floor. The researchers propose an operating system that incorporates an eye-in-hand system with a touchscreen interface for a robotic arm. This system enables users to specify the target position by drawing a line on the touchscreen interface, facilitating efficient grasping and delivery of objects. Compared to a conventional on-screen joystick, the proposed interface proves to be quicker and more effective, reducing the physical burden on users. Additionally, the proposed interface introduces a system that utilizes a 2D camera for a 6 DOF robotic arm, myCobot 280 M5, mounted on an electric wheelchair, allowing users to retrieve objects from the floor through visual instructions. Experimental comparisons reveal that this interface significantly reduces the burden on operators and improves operation completion time. The system offers a practical solution for patients with trunk dysfunction, enabling them to independently retrieve objects without relying on caregivers.Topic: MetaPo: A Robotic Meta Portal for Interspace Communication
Author: Takuro Yonezawa, Nozomi Hayashida, Kenta Urano, Johannes Przybilla, Yutaro Kyono
Abstract: The authors introduce MetaPo, a mobile robot with spheric display, 360°media I/O,6 DOF robotic arm myCobot and robotic hands for creating a unified model of interspace communication. MetaPo works as a portal between pairs of physical-physical, cyber-cyber and cyber-physical spaces to provide panoramic communication for multiple remote users, and immersive interspace migration with mobility functionality. The paper overviews the concept and first prototype of MetaPo with its hardware and software implementation.Topic: ROMI: A Real-Time Optical Digit Recognition Embedded System for Monitoring Patients in Intensive Care Units
Author: Sanghoon Jeon 1,Byuk Sung Ko 1, and Sang Hyuk Son 2
Abstract: The article discusses the need for constant monitoring of ICU patients, especially during the COVID-19 pandemic, where non-face-to-face monitoring is crucial. The proposed solution is ROMI, a real-time optical digit recognition embedded system integrated into a mobile robot composed of myAGV and myCobot 320. Developed using Matlab Simulink, ROMI achieved a high digit recognition performance of 0.989 mAP on alexnet. It was deployed on NVIDIA GPU embedded platforms for practical use. The system's potential impact lies in supporting medical staff with non-face-to-face monitoring in ICUs, ensuring more effective and prompt patient care. The article details the development of ROMI, its functions, and the evaluation of its performance on different GPU platforms, emphasizing its significance in addressing the challenges of ICU patient monitoring.Topic: Towards the Cognitive Factory in Industry 5.0: From Concept to Implementation
Author: Wagner Augusto Aranda Cotta 1,2 ,Sergio lvan Lopes 1,3 and Raquel Frizera Vassallo 2
Abstract: This article explores the convergence of Industry 5.0 (I5.0) and Intelligent Systems (IS) through the creation of a cognitive cell replica in a lab. Focusing on the safe collaboration between humans and 6 DOF robotic arm myCobot 320 Pi, the study addresses technical challenges in implementing a cognitive factory. The developed cognitive cell demonstrates the integration of OT and IT networks, a customized communication model, and device interoperability, serving as a test bed for applications within the cognitive factory. Experiments confirm the system's effectiveness, showcasing its ability for multiple operations and accuracy in tasks like color recognition and human localization. It emphasizes the transformative potential of cognitive factories, providing insights for future research and contributing to the advancement of Industry 5.0 principles.Topic: On the Sense of Unity Generated from Physical Cooperation between Human and Robot
Author: Takuro Sumida†1, Sojiro Kamimura†1 , Koaki Hasegawa†1 , Michio Okada†1 , Naoki Oshima†2
Abstract: This paper delves into fostering a sense of accomplishment and unity through collaborative endeavors between humans and robots. The authors introduce the "Balance Board," a board game designed to serve as a mediator, creating a "side-by-side relationship" between humans and the 6 DOF robotic arm myCobot 280 M5. The game establishes a cooperative environment where both entities collaborate, fostering a sense of oneness. The paper details the board game's development and outlines future interactive experiments to validate the significance of effective communication, including vocal and gestural cues, to enhance the cooperative experience. Ultimately, this work aims to facilitate a harmonious and productive relationship between humans and robots.Topic: REPROGRAMMING OF AN AGV TO EXPAND ITS FUTURE AUTOMATION AND CONNECTIVITY
Author: Miriam Conde Montoya University: Universitat Politècnica de Catalunya
Abstract: The project focuses on utilizing an AGV (Automatic Guided Vehicle) to capture and process the robot's data using MATLAB. The primary goal is to develop an application that presents myAGV's 2D mapping of the space, including the route taken and images captured by the robot's camera corresponding to its kinematic model's position the detailed real routes and images captured by the AGV's cinematic model. The application not only visualizes the data but also caters to the needs of users with limited MATLAB proficiency, making it a versatile tool for various projects. Ultimately, the project successfully achieved its main objective, resulting in a user-friendly application that enables individuals with limited MATLAB knowledge to visualize and analyze AGV-captured data for the specific projects.Topic: SISTEMA DE GESTIÓN Y CONTROL REMOTO DE UN ROBOT AGV PARA APLICACIONES EN ALMACENES.
Author: Marc Nueno Montolio University: Universitat Politècnica de Catalunya
Abstract: For many companies, warehouse automation is becoming a process key to improving efficiency, reducing costs and increasing safety. In this process, AGV mobile robot is a fundamental robotic tool. The project focused on developing a remote control and management system for a mobile robot myAGV tailored for warehouse automation. During the implementation of the project, the real-time data from Lidar, 2D camera, and myAGV sensors enabled successful navigation, goods transportation, and automated inventory management. In a parallel experiment, the feasibility of implementing a robot arm for product transfer to a quality control system, specifically for MSMEs, was assessed. The project achieved its goal by utilizing real-time data, implementing a ROS platform, and developing programs for easy teleoperation and autonomous inventory.Topic: Robot-enabled tangible virtual assembly with coordinated midair object placement
Author: Li Zhang 1, Yizhe Liu 1, Huidong Bai 2, Qianyuan Zou 2, Zhuang Chang 2, Weiping He 1, Shuxia Wang 1, Mark Billinghurst 2
Abstract: The assembly in Virtual Reality (VR) enables users to fit virtual parts into existing 3D models immersively. However, users cannot physically feel the haptic feedback when connecting the parts with the virtual model. This paper presents a robot-enabled tangible interface that dynamically moves a physical structure with a robotic arm to provide physical feedback for holding a handheld proxy in VR. This enables the system to provide force feedback during virtual assembly. The cooperation between the physical support and the handheld proxy produces realistic physical force feedback, providing a tangible experience for various virtual parts in virtual assembly scenarios. The authors developed a prototype system that allowed the operator to place a virtual part onto other models in VR by placing the proxy onto the matched structure attached to a 6 DOF robotic arm. THey conducted a user evaluation to explore user performance and system usability in a virtual assembly task. The results indicated that the robot-enabled tangible support increased the task completion time but significantly improved the system usability and sense of presence with a more realistic haptic experience.Topic: Application of Robot Arm Control System for Fruit Harvesting Based on Deep Learning and Binocular Vision
Author: DENG-YUNG HUANG 1 and JING-MAU SHIU 2
University: Da-Yeh University 1,Hong-Sin-Ke Automatic Automation Co., Ltd. 2
Abstract: This paper focuses on developing an effective and cost-efficient robotic arm control system for fruit-picking robots by leveraging computer vision and deep learning techniques. The proposed system integrates the YOLOv5 object detection model and an OAK-D stereo camera for depth estimation, enabling accurate object localization without relying on expensive distance sensors. To enhance the adaptability of the system, the authors propose Fine-tuning training for the YOLOv5 model, enabling customization for different fruits and scenarios. The goal is to embed the developed system into edge computing devices, achieving lightweight loads for efficient operation. The combination of the object detection model, binocular camera, and robotic arm control ensures quick and effective generalization for various usage scenarios. Experimental results indicate the success of the proposed system in controlling a robotic arm using low-cost sensors, making it a viable solution for widespread application in robotic arm control systems.Topic: Computational Systems Design of Low-Cost Lightweight Robots
Author: Akhil Sathuluri, Anand Vazhapilli Sureshbabu, Jintin Frank, Maximilian Amm andMarkus Zimmermann
Abstract: The paper addresses the growing demand for task-specific robots, emphasizing the preference for collaborative robots. It introduces a top-down computational design strategy for developing low-cost and lightweight modular robots. This involves exploring the design space for robot modules and optimizing structural elements to significantly reduce weight. The paper highlights non-intuitive robot architectures and demonstrates a 16% reduction in structural mass compared to conventional designs. It introduces custom-designed modules, discusses material selection and manufacturing choices, and suggests future research directions. The conclusion advocates for applying the method to industrial-scale robots and benchmarking for general design guidelines.Topic: Exploring a Unique Design Tool for Close Proximity Human-Robot Collaboration
Author: Yi Zhao,Lian Loke,Dagmar Reinhardt
University: The University of Sydney
Abstract: The research endeavors to fill the gap in design tools for designers involved in creating robots and human-robot collaboration (HRC) tasks. Adopting a research-for-design approach, a preliminary HRC design tool is crafted based on the leader-follower model, tailored for close-proximity collaboration. This tool is specifically crafted for co-drawing applications utilizing augmented reality and diverse cobots, aiming to contribute fresh insights to the HRC community. The study delves into the dimensions of human-robot interactions within design tools, focusing on collaborative activities. Constructed through a research-for-design approach and refined via the research-through-design methodology, with a case study on collaborative drawing, the HRC design tool caters to designers without prior robotic development experience. It facilitates exploration and specification of human-robot interactions. Future work includes user workshops, design AR-based co-drawing projects with 6 DOF desktop robotic arm myCobot 280 Pi, and continuous improvement based on iterative evaluation.
Topic: Basic Study on IoT Security Using Robot Arm
Author: Shu Takemoto 1, Yoshiya Ikezaki 2, Yusuke Nozaki 3, Masaya Yoshikawa 4
University: Meijo University
Abstract: The paper addresses the growing integration of IoT devices in industrial systems for Industry 4.0, emphasizing the need for secure IoT systems in the face of cyber threats. It highlights the Lightweight Cryptography Competition's role in selecting potential cryptographic standards for IoT, with Ascon being chosen as a standardized cipher. The study focuses on evaluating encryption and authentication techniques using Ascon, specifically investigating IoT security using state-of-the-art lightweight cryptography in the world's smallest and lightest 6 DOF robotic arm myCobot 280. The research investigates communication schemes for python, a common development scheme in myCobot 280, and implements Ascon for low-latency and secure communication. The study conducts real-device evaluations on myCobot, providing insights into the performance and implementation overheads of secure communication in an IoT system.Topic: MECHANICAL DESIGN OF A MOBILE COLLABORATIVE ROBOT USING A PLANETARY GEAR SYSTEM
Author: Ángel De la Cruz Martínez
University: Higher Technological Institute of Atlixco
Abstract: This thesis report outlines the design process of a collaborative mobile robot (Cobot) with a focus on the mechanical structure. Cobots are designed for human interaction in shared workspaces without requiring safety fences, and their applications range from part classification to risk detection in industrial settings. The project proposes the design of a mobile robot incorporating a 6 DOF collaborative robot myCobot 280 Pi with a planetary gear system, efficiently preserving torque-speed characteristics. This endeavor is part of a larger research project funded by the National Technological Institute of Mexico (TecNM) 2022, aiming to develop mobile Cobot applications using contemporary technologies such as ARM microcontrollers and IoT communication systems. The proposed mechanical design, featuring a planetary gear system, considers not only gear geometries but also the supporting axles, enhancing the overall understanding of the transmission system. The project is seen as having significant potential for implementation and manufacturing, with the next phase involving the physical development and creation of a real prototype.
Topic: Laboratory hollyhocks for robotic arm Dobot Magician Department of process control
Author: Tomáš Vladyka
University: University of Pardubice
Abstract: This peper's thesis focuses on creating educational laboratory tasks tailored for teaching students how to operate the Dobot Magician robotic arm. The tasks cover theoretical aspects, wiring diagrams, and solution procedures, catering to beginners in robot programming. The theoretical section provides an overview of robotic arms, with emphasis on the Dobot Magician. Practical training includes exercises on basic movements, Python programming, input/output control, and connecting expansion modules. The goal is to guide students from basic familiarity to developing control applications using DobotStudio, Visual Studio, or Arduino IDE. The tasks, tested successfully at the University of Pardubice and a secondary industrial school, received positive feedback for being well-written and detailed. While the thesis introduces Dobot robotic vision, the complexity of solution procedures necessitates a separate set of tasks for programming vision systems and image recognition using DobotVisionStudio.
This curated collection of academic papers is a journey through groundbreaking research, exploring innovative design tools for close proximity human-robot collaboration and the nuanced integration of proximity sensors in commercial robotic arms. Elephant Robotics will strive to continuously innovate and provide superior robotic products to meet evolving market needs and cultivate an environment of continuous robotics innovation.